For construction executives, one of the primary concerns is managing the cost of materials and labor. Unfortunately, in recent times, these costs have been rising steadily, which can put a strain on budgets and profitability. However, there are still ways to keep these costs down, even in a market where prices are increasing. Here are some tips to help you manage your costs effectively:
- Build Strong Relationships with Suppliers – One of the best ways to keep costs down is by building strong relationships with your suppliers. This can help you negotiate better prices and terms, and also ensure that you receive priority service and delivery. Try to work with suppliers who are willing to offer you volume discounts or special deals for repeat business. You can also explore the possibility of buying in bulk to reduce per-unit costs.
- Track Prices and Trends – Another important aspect of cost management is tracking prices and trends in the market. By monitoring price changes and fluctuations, you can anticipate cost increases and adjust your budget accordingly. You can also take advantage of opportunities to buy materials or hire labor at lower prices when they become available. This requires staying informed about the latest industry news and developments.
- Optimize Your Supply Chain – To reduce costs, it’s important to optimize your supply chain. This means streamlining your procurement process, reducing the time it takes to order and receive materials, and improving logistics and transportation. You can also explore the use of alternative suppliers and vendors to find better deals and improve delivery times.
- Improve Your Planning and Scheduling – Another way to keep costs down is by improving your planning and scheduling processes. By better coordinating materials and labor, you can reduce waste and inefficiencies, and ensure that work is completed on time and on budget. This requires careful planning and communication between different teams and stakeholders, as well as effective project management tools and software.
- Invest in Training and Education – Finally, investing in training and education can help you reduce costs over the long term. By improving the skills and knowledge of your workforce, you can increase efficiency, reduce errors and waste, and improve overall quality. This can lead to lower costs and higher profitability over time, as well as a better reputation and stronger customer relationships. In addition to these general tips, there are also some specific strategies you can use to manage costs for materials and labor.
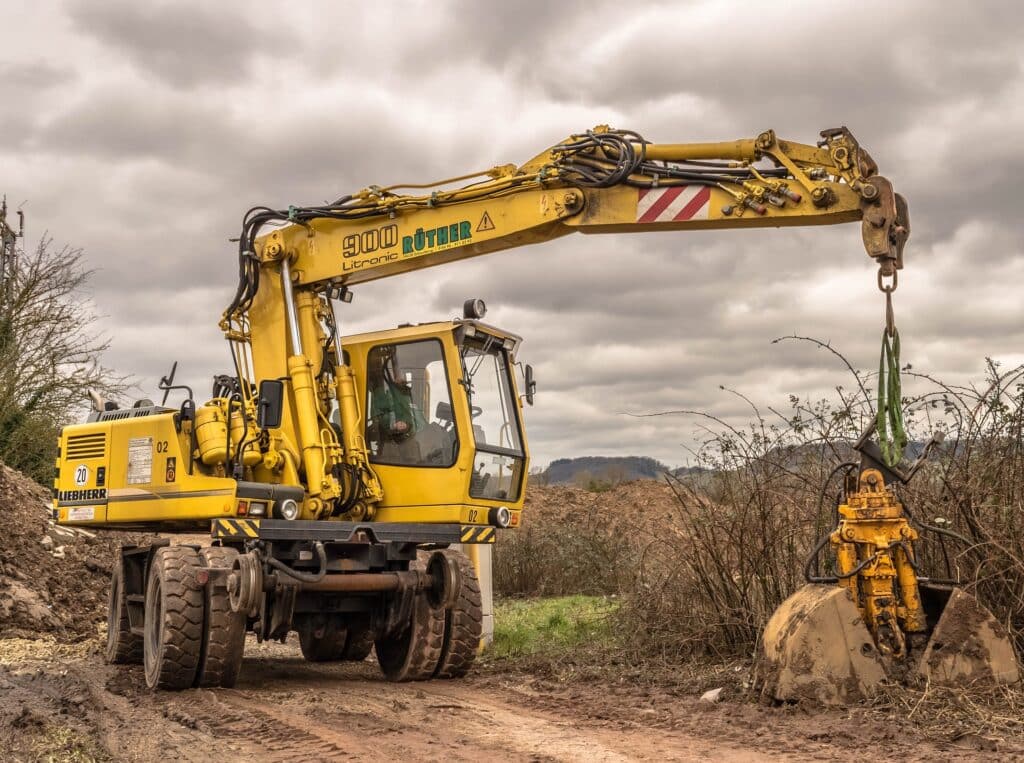